Biological drugs that fall under the definition of Advanced Therapies Medicinal Products (ATMP) are drugs that, by their nature, cannot be sterilized. For this reason, the production process must be conducted aseptically, to prevent any possible contamination.
The main risks of aseptic production of ATMPs in a cleanroom are due to the presence and movement of operators and the absence of physical barriers between product and operator. If the production takes place in a closed system, such as an isolator, the transfer of materials becomes a critical element. The transfer of materials inside and outside the isolator is in fact one of the main potential sources of contamination and appropriate control measures must be considered. When materials are introduced/removed from the closed system without an aseptic connection, the system can no longer be considered closed. In order to reduce the risk of contamination, the best solution should be to transfer biological samples from a Grade A (ISO 4.8) isolator to external standard CO2 incubators, and vice versa, without breaking the continuity of bio-confinement.
BioBoxβ, a solution patented by BioAir Spa, uses a synergistic combination of known technologies that together contribute to making the system functional for the transfer of biological samples from a Grade A (AinD) isolator to external standard CO2 incubators, and vice versa, without breaking the continuity of the insulation. BioBoxß containers are equipped with a Beta RTP port. The RTP port is based on the principle of the double door: the Alpha port, fixed on the isolator chamber, and the Beta port (present on the BioBoxß), which is equipped with the transfer canister. The doors cannot be opened until their flanges are not connected to each other. The RTP is recognized as a validated system for the entry and transport of material to/from production isolators in regulated environments.
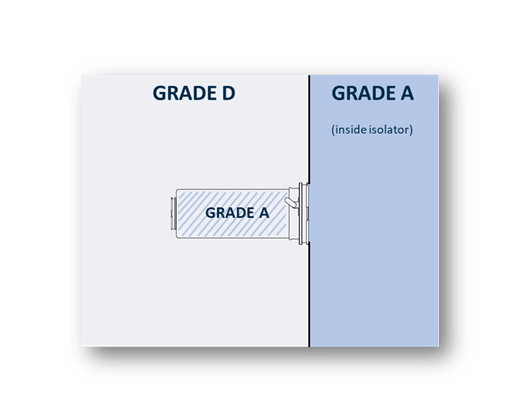
Once connected to the isolator, the biological samples (normally contained within flasks) can be introduced inside the BioBoxß, which will then be closed and disconnected (always without breaking the continuity of the insulation) from the Isolator to be transferred to an external CO2 Incubator, as shown in the figure. The return of the samples, from the external CO2 incubator to the isolator – for any further manipulation after incubation – is carried out with the same procedure.
The filter cartridges permeable to gases present in the BioBoxß allow the cells contained in the flasks to exchange gases if placed inside an external standard CO2 incubator. Finally, the filter cartridges, which will be sterilized after use for a single patient/cell batch, avoid cross-contamination between samples of different patients even if incubated in the same CO2 Incubator, in different BioBoxß.
The use of this innovative system offers several advantages, such as the elimination of integrated or external CO2 incubators with docking systems, very expensive and complex to manipulate. It also allows you to work in a GMP environment with standard CO2 incubators outside the isolator located in the Grade D clean room, ensuring transit in the Grade D area of the BioBoxß without contaminating the inside (H14 filters). Finally, the use of this system for each individual patient allows eliminating cross-contamination between samples from different patients even if the samples are placed in the same CO2 incubator.
ATMP’s closed systems for aseptic production are flexible, economical, and sustainable tools: some of their limits can be overcome thanks to technological innovation and the development of accessories, designed ad hoc.
Adapted from the work of C. Zanini, F. Severina, A. Rossi; available on: Sistemi di trasferimento a tenuta per isolatori
Recent Articles
- Cell therapy based on neuronal precursors for the treatment of multiple sclerosis 10 January 2023
- How to Improve the Sustainability of Advanced Therapies: The Case of Strimvelis 24 November 2022
- FDA reorganization: a “Super Office” to manage the increasing cell and gene therapy workload 3 November 2022
- GMP Cleanliness Classifications: Deciphering the Differences and Requirements among Grades 12 September 2022
- How to Overcome the Most Common Issues in the GMP-Compliant Culturing of Mesenchymal Stem Cells: Isolation and Automatization 30 August 2022