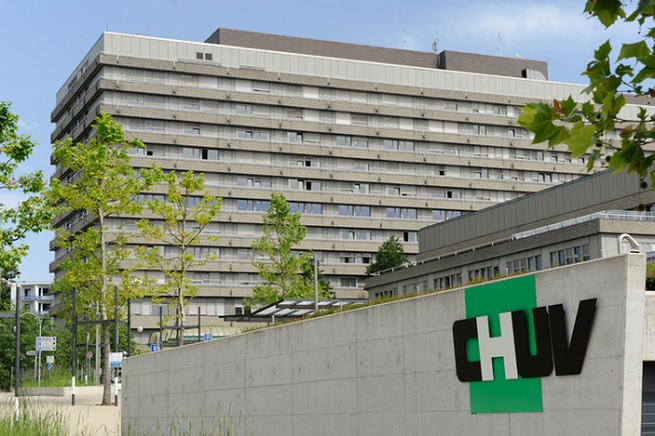
The Centre Hospitalier Universitaire Vaudois (CHUV) is one of the most important hospitals in the world, with more than 48,000 patients per year and approximately 12,000 employees. In 2019, Newsweek Magazine rated the CHUV as the 9th best hospital in the world1.
Among the several departments present in the hospital complex, one of the most intriguing and innovative is represented by the Cell Production Center (CPC), headed by Dr. Jean-François Brunet. The CPC, initially established in the 80s to develop therapeutic cultured cellular product protocols for severe burned patients, has been extensively implemented in recent years, adding new facilities and different objectives. Today, thanks to the recent findings that revolutionized the field of biotechnology and with the rising of the Advanced Therapy Medical Products (ATMPs), the main purpose of the CPC is to develop and elaborate autologous and allogeneic cell therapies for several different types of diseases. Other than the creation of fist cover bandages made of autologous fibroblast, the CPC is mainly focused on the development of autologous chondrocytes for orthopedics purposes, the research on stem cell applications, the culture of epidermal or dermo-epidermal autografts, and others.
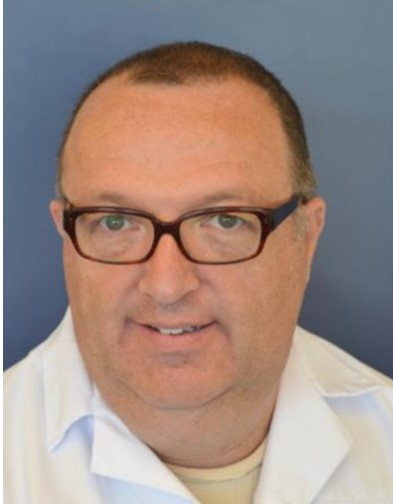
Head of Cell Production Center
As mentioned, CPC is specialized in cell production and manufacturing for autologous transplantation of fibroblasts and epidermal tissue to sever burned patients, and in this field is one of the most important centers in the world. To ensure the synergistic collaboration of various professionals gravitating around burn care, the careful management of risks and costs is fundamental. This involves the design of the facilities, the meticulous examination of every aspect of cell therapy, and stringent adherence to the GMP guidelines. For these reasons, in 2012, Dr. Jean-François Brunet and his team chose to modify the GMP facility of CPC, applying a Closed System design to the clean rooms with the installation of six BioAir’s ATMP Isolators.
A Closed System is formed by an isolated self-standing environment physically separated from the rest of the clean room. Biomaterials and other components are manipulated through gloves affixed to the enclosure surrounding of the critical zone; practically the gloves can be considered in direct continuity with the external glass. Preliminary cleaning and glove installation are performed nonaseptically and the isolator is automatically decontaminated before starting the process. Component addition is performed without opening the isolator using specifically designed batch transfer systems for ingress/egress. The isolator always maintains a positive pressure and is never opened during use. Considering those peculiar characteristics, Isolators are allowed to work in a Class D external environment, with a significant reduction in the maintenance costs (more than 65% if compared to an open system), but also with a decrease in the validations timings. Moreover, Isolators allow to speed-up the production, increasing at the same time the safety of both operators and products2.
According to eudralex part IV annex I, the “[…] Isolators are beneficial in assuring the required conditions and minimizing the microbial contamination associated with direct human interventions in the critical zone. Their use should be considered in the CCS. Any alternative approaches to the use of […] Isolators should be justified.”3 So if for a given system, the choice was to use an open system instead of an Isolator, this alternative approach should be justified.
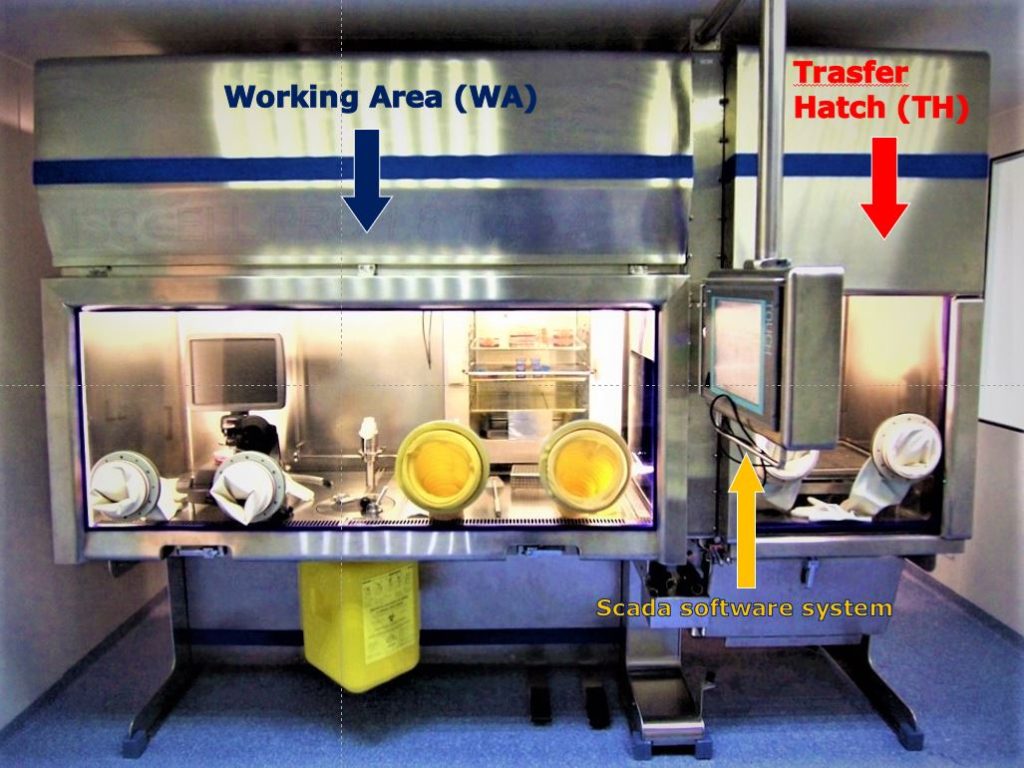
As mentioned, the GMP facility of CPC is using six BioAir’s ATMP Isolators to generate a workflow within a bioconfinement Grade A setting, entirely surrounded by a Grade D environment. As confirmed by the work “Burn Center Organization and Cellular Therapy Integration: Managing Risks and Costs”, the closed system AinD design requires less overall maintenance, less personnel, and less cleaning procedures than a standard open system AinB cleanroom4.
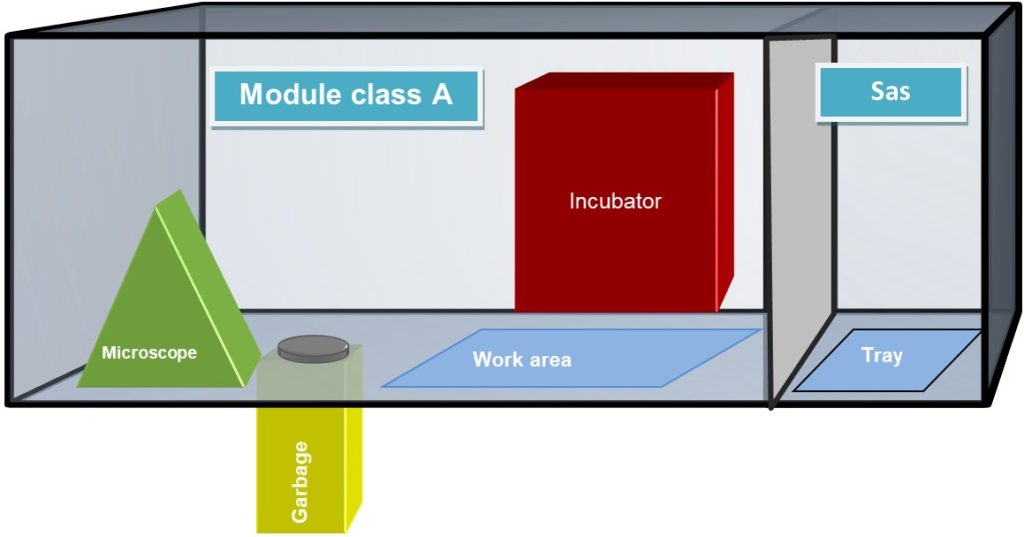
A classical open system clean room is formed by a series of environments one inside the other, starting from an unclassified area to Grade D, then grade C, and the real clean room in grade B; an enormous and complicated layered structure. Other than the tremendous amount of space required, the process of entering the Grade B room can be laborious and tricky and can last for more than one hour. In a closed system clean room, as the one present in CPC, the biological samples and all the required material is transferred directly from an unclassified hallway to the Grade D clean room through a material transfer hatch. Prior, during, and after the manufacturing process, everything step, material, or passage is accurately registered both by the isolator itself and by SCADA software installed on a monitor near the work area of each isolator. In this way, all the production passages are faster than in an open system clean room, and easily recorded.
According to the latest available data, the maintenance cost of a closed system clean room is one-third of the cost of an open system clean room in the same area. This is mainly due to a significant reduction in energy expenses, extremely important nowadays.
In conclusion, the decision of one of the most important centers for ATMP production to move from a classical open system design to a closed system through the installation of six ATMP Isolators is justified not only by GMP guidelines, but also by a significant reduction of the maintenance costs, a fundamental increase in the safeties of both the bio-products and the operators, and a subsequent speed-up of the production. This is why several important observers already consider Isolators and closed systems as the future of clean rooms for Advanced Therapies.
To have further information regarding the CPC center, the CHUV hospital, or the works of Dr. Jean-François Brunet please visit the website of CHUV hospital (https://www.lausanneuniversityhospital.com/home) or read their works at https://pubmed.ncbi.nlm.nih.gov/33970273/, and at https://www.lausanneuniversityhospital.com/healing-severe-burn-victims.
References
1. Miller N. The 10 Best Hospitals in the World. Newsweek. 2019;172(10). Accessed July 8, 2022. https://www.newsweek.com/2019/04/05/10-best-hospitals-world-1368512.html
2. Zanini C, Severina F, Lando G, et al. Good design practices for an integrated containment and production system for advanced therapies. Biotechnol Bioeng. 2020;117(8):2319-2330. doi:10.1002/bit.27376
3. European Commission. Annex 1 : Manufacture of Sterile Products Document map. Published online 2010.
4. Chemali M, Laurent A, Scaletta C, et al. Burn center organization and cellular therapy integration: Managing risks and costs. J Burn Care Res. 2021;42(5):911-924. doi:10.1093/jbcr/irab080
Recent Articles
- Cell therapy based on neuronal precursors for the treatment of multiple sclerosis 10 January 2023
- How to Improve the Sustainability of Advanced Therapies: The Case of Strimvelis 24 November 2022
- FDA reorganization: a “Super Office” to manage the increasing cell and gene therapy workload 3 November 2022
- GMP Cleanliness Classifications: Deciphering the Differences and Requirements among Grades 12 September 2022
- How to Overcome the Most Common Issues in the GMP-Compliant Culturing of Mesenchymal Stem Cells: Isolation and Automatization 30 August 2022